Optimiser un système d'air comprimé avec une demande d'air très fluctuante
Résumé
Lorsqu'un système d'air nécessite de grandes quantités d'air (environ >100 m3/min) et que la demande d'air fluctue fortement au cours de la journée, les utilisateurs finaux pensent généralement que les grands compresseurs à vis à vitesse variable peuvent permettre de réaliser d'importantes économies en adaptant précisément le débit d'air comprimé à la demande du système.
Prenons l'exemple de la figure 1. Lorsque la demande quotidienne de débit varie jusqu'à 90 % de la demande maximale d'air, l'étude compare la consommation d'énergie de six solutions alternatives en termes de nombre de compresseurs installés, de tailles de compresseurs et de types de technologies de compression (c'est-à-dire centrifuge sans huile et rotative sans huile).
Fig. 1 : Profil de débit à haute variabilité (90 pour cent) pour une période de 24 heures.
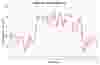
L'influence du système de contrôle d'un compresseur d'air et de ses différentes logiques de contrôle est également prise en compte dans l'analyse.
La consommation d'énergie des six mêmes solutions est ensuite comparée avec différents modèles de demande d'air pour simuler le comportement des six systèmes dans le cas de besoins de production variables (c'est-à-dire que les quatre autres modèles de demande d'air quotidiens avec une variabilité différente sont également pris en compte).
CHOISIR LA BONNE SOLUTION D'AIR COMPRIMÉ
Il existe différentes technologies de compression et chacune d'entre elles peut présenter ses propres avantages et inconvénients, en fonction de l'application particulière, de la plage de fonctionnement, de la puissance, de la capacité et d'autres aspects.
Néanmoins, lorsqu'un système d'air nécessite de grandes quantités d'air et que la demande d'air fluctue fortement au cours de la journée, les utilisateurs finaux pensent souvent que seule l'utilisation de grands compresseurs à vis à vitesse variable permet de réaliser d'importantes économies en adaptant exactement le débit d'air comprimé fourni à la demande d'un système.
L'objectif de cette étude est de comparer et d'évaluer six solutions d'air comprimé différentes lorsque la demande d'air est très fluctuante. L'étude a pris en compte cinq profils de débit variable, tels que décrits dans les figures 1 à 5, afin de définir quelques lignes directrices pour aider les utilisateurs finaux à sélectionner le système le mieux adapté à leur application.
ÉTUDES DE CAS CONNEXES
Dans le cas n° 1 (figure 1-2), la demande d'air fluctue fortement entre les quarts de nuit et de jour, passant d'environ 30 m3/min à 220 m3/min, ce qui représente une variabilité de 90 % du débit.
La figure 2 définit plus précisément le profil de débit dans le cas n° 1. L'axe des y représente le débit de la demande en chiffres absolus à gauche, et en pourcentage du débit maximal demandé au système à droite. L'axe des abscisses indique le temps en pourcentage de la période d'observation totale. Compte tenu de ces données, le chercheur peut déduire que l'installation représentée dans le cas n° 1 fonctionne en dessous du débit moyen près de 50 % du temps. Ce spectre de débit est typique d'un site de production avec deux équipes de nuit de six heures avec une faible demande d'air et deux équipes de jour de six heures avec une forte demande d'air.
Fig. 2 : Spectre de débit à haute variabilité (90 %)
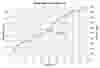
Les quatre autres cas analysés sont décrits dans les figures 3 à 6 et sont représentatifs :
Cas n° 2 (Fig. 3) : Un autre spectre très variable avec 90 % de variabilité mais, par rapport au cas n° 1, un débit inférieur au débit moyen n'est demandé que 30 % du temps. Ce spectre est typique d'une production avec une équipe de nuit de huit heures avec une faible demande d'air et deux équipes de jour de huit heures avec une forte demande d'air.
Fig. 3 : Profil de débit à haute variabilité (90 pour cent) pour un temps moyen
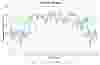
Cas n° 3 (Fig. 4) : Similaire aux cas n° 1 et n° 2 mais avec une variabilité plus faible qu'auparavant (environ 65 % du débit maximum au lieu de 90 %). Pour le différencier des deux cas précédents, nous l'appelons cas de variabilité moyenne. Comme pour le cas n° 1, cette variabilité se produit pendant une longue période, puisque le débit demandé est inférieur au débit moyen pendant environ 50 % du temps.
Cas n° 4 (Fig. 5) : Un schéma de débit à variabilité moyenne (environ 65 % du débit maximal, comme dans le cas n° 3) ; par rapport au cas n° 3, un débit inférieur au débit moyen n'est demandé que 30 % du temps.
Cas n° 5 (Fig. 6) : Un schéma de débit à faible variabilité avec une variabilité d'environ 30 % seulement du débit maximal tout au long de la journée, représentatif d'une production quasi constante 24 heures sur 24.
DES SOLUTIONS DE COMPRESSEUR ÉCONOMES EN ÉNERGIE
Du point de vue de la consommation d'énergie, il existe six solutions alternatives de compresseurs pour les situations décrites dans les cas 1 à 5 :
- Solution A considère un compresseur centrifuge et un grand compresseur à vis à vitesse variable (700 kW) dont le débit maximum est égal à la moitié de la demande de débit maximum du système.
- Solution B utilise deux compresseurs centrifuges dont le débit maximal est égal à la moitié de la demande de débit maximale du système. Il est connu que les compresseurs centrifuges peuvent être conçus pour une efficacité optimale avec une plage de régulation réduite ou une plage de régulation étendue, également appelée "turndown", avec une efficacité de conception plus faible. Dans cette seconde solution, les compresseurs sont conçus pour une efficacité maximale et disposent du contrôle de répartition de charge le plus récent et le plus efficace.
- Solution C utilise deux compresseurs centrifuges conçus avec une large plage de régulation. Dans cette solution, comme dans toutes les solutions suivantes avec plusieurs compresseurs centrifuges, les compresseurs centrifuges sont équipés d'un système de contrôle de la répartition de la charge, car ce système de contrôle permet toujours de réduire le débit des compresseurs centrifuges en étendant la plage de régulation du système.
- Solution D considère trois compresseurs centrifuges dont le débit maximum est un tiers de la demande de débit maximum du système. Il est conçu pour une large réduction et un contrôle de la répartition de la charge.
- La solution E envisage des technologies mixtes, mais dans ce cas, il y a deux compresseurs centrifuges avec contrôle de la répartition de la charge et un petit compresseur à vis à vitesse variable (160 kW). Dans ce scénario, les compresseurs ne sont pas contrôlés par un programmateur. Cela signifie que le petit compresseur à vis à vitesse variable n'est utilisé que pour couvrir les pics de demande d'air.
- La solution F utilise les mêmes compresseurs que la solution E, mais dans ce cas, les trois compresseurs sont contrôlés par un planificateur. Le programmateur permet au système de faire fonctionner - par exemple, de charger, décharger ou éteindre - chaque compresseur selon un programme prédéfini afin d'optimiser le système de différents points de vue ; dans ce cas, du point de vue de la consommation d'énergie.
Pour revenir à notre profil de débit original de la figure 1, la solution A - avec un compresseur centrifuge et un grand compresseur rotatif à vitesse variable - peut correspondre exactement au débit demandé par le système. C'est pourquoi il s'agit d'une combinaison imbattable, car il n'y a pas de gaspillage d'air. Néanmoins, nous devons déterminer s'il s'agit également de la solution la plus efficace du point de vue de la consommation d'énergie. L'utilisation d'un seul compresseur centrifuge avec un débit maximal égal à la demande maximale du système n'est pas une solution viable en raison de la grande quantité d'air gaspillé, comme le montre la figure 4. C'est pourquoi cette configuration n'a pas été retenue parmi les solutions examinées précédemment.
Fig. 4 : Soufflage d'air avec un seul compresseur centrifuge de 220 m3/min
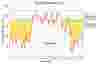
Lorsque plusieurs compresseurs centrifuges sont installés dans un système, il est possible de réduire le soufflage des compresseurs centrifuges en installant un système de contrôle de la répartition de la charge. Les figures 8 et 9 montrent la différence, en termes de plage de régulation, entre deux compresseurs identiques, dont le débit maximal est égal à la moitié de la demande d'air maximale du système, sans et avec un système de contrôle de la répartition de la charge.
Fig. 5 : Soufflage d'air avec deux compresseurs centrifuges de 110 m3/min sans contrôle de la répartition des charges
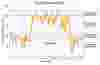
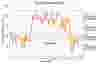
Dans le cas d'une demande de débit variable dépassant la plage de régulation naturelle - également appelée "turn-down" - d'un compresseur centrifuge, l'utilisation d'un système de contrôle de répartition de la charge de pointe est toujours bénéfique lorsque deux compresseurs centrifuges ou plus sont utilisés dans un système, car elle permet de réduire les pertes d'air.
Chacune des solutions décrites dans les solutions B à F permet au système d'avoir une quantité différente d'air perdu. Dans certains cas, comme celui de la solution F (Fig. 7), l'évacuation de l'air est minime. Elle est très proche de la solution A, qui utilise un compresseur centrifuge et un grand compresseur à vis à vitesse variable. Néanmoins, ce n'est pas la minimisation des pertes d'air qui détermine les meilleurs systèmes, mais la minimisation de la consommation d'énergie.
Fig. 7 : Dans la solution F, soufflage d'air avec deux compresseurs centrifuges de 100 m3/min conçus pour une efficacité maximale avec contrôle de la répartition des charges, plus un compresseur à vis à vitesse variable de 25 m3/min (160 kW) avec programmateur
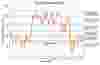
En considérant les performances à une pression de 8 barg pour chacun des compresseurs utilisés dans les solutions A à F, la figure 8 montre la comparaison de la consommation d'énergie quotidienne pour le schéma d'écoulement du cas n° 1 avec une forte variabilité pendant une longue période. Il montre également l'efficacité relative entre la solution A - la solution imbattable - et les cinq autres solutions. L'efficacité de la solution A est prise comme référence et est égale à 100.
Fig. 8 : Comparaison des systèmes, consommation d'énergie quotidienne
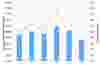
La solution A n'est pas imbattable, mais la solution F - composée de deux compresseurs centrifuges avec répartition de la charge et d'un petit compresseur à vis à vitesse variable de 160 kW avec un programmateur - est la meilleure solution en termes d'économie d'énergie. La solution F permet à l'utilisateur d'économiser près de 3 % par rapport à la solution A.
La solution C - configurée avec deux compresseurs centrifuges conçus avec une large plage de régulation et un contrôle de la répartition de la charge - malgré une certaine perte d'air, n'est que 0,3 % moins efficace que la solution A ; c'est donc une option préférable du point de vue de l'exploitation. En fait, si l'on considère 300 jours de fonctionnement par an et un coût énergétique moyen de 0,10 €/kWh (0,13 $/kWh), la solution A permet aux opérateurs d'économiser seulement 1 500 € (19 500 $) par an par rapport à la solution C. Ces économies ne justifient pas les inconvénients de fonctionnement de ce système : La solution A utilise deux compresseurs avec des pièces de rechange complètement différentes, et si un compresseur de secours est nécessaire, un seul peut être choisi, ce qui ne garantit pas la même efficacité de fonctionnement. La solution C, qui consiste à utiliser deux compresseurs centrifuges identiques, élimine ces deux problèmes.
La figure 9 montre la comparaison des coûts annuels d'énergie pure¹ des six solutions de compresseur dans le cas d'un modèle de flux d'air, comme dans le cas n° 1. Une autre considération importante est d'évaluer le comportement des six solutions au cas où des changements de production futurs affecteraient la consommation d'air quotidienne.
Fig. 9 : Comparaison des coûts énergétiques annuels dans le cas n° 1.
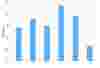
Les schémas d'écoulement des cas n° 2 à 5 représentent différents profils d'écoulement d'air variables dans diverses conditions de production, qui couvrent presque toutes les solutions - de la plus variable à la moins variable - comme l'illustrent les figures 3 à 6.
Le tableau 1 résume les efficacités relatives entre la solution A et les cinq autres solutions avec des profils de débit variables, comme dans les cas n° 1 à 5.
Tableau 1 : Comparaison de l'efficacité énergétique : L'efficacité de la solution A est utilisée comme référence. Les pourcentages rouges ou orange négatifs indiquent que le système est moins efficace que la solution A, et les chiffres positifs et verts indiquent que le système est plus efficace que la solution A. Le jaune signifie que les deux systèmes sont plus ou moins égaux. La dernière ligne indique le classement des six solutions en fonction de l'efficacité du système (ou des coûts énergétiques annuels), de la flexibilité et de la facilité d'utilisation, c'est-à-dire des pièces de rechange communes et d'un compresseur de secours tout aussi efficace.
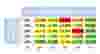
Considérons à nouveau les performances d'un compresseur à une pression de 8 bar, 300 jours de fonctionnement par an et un coût énergétique moyen de 0,10 €/kWh (0,13 $/kWh). La solution F permet aux opérateurs d'économiser 15 000 € (19 500 $) par an dans le cas n° 1 et environ 4 000 € (52 000 $) par an dans le cas n° 5, par rapport à la solution A. La solution C a des coûts énergétiques légèrement plus élevés, environ 1 500 € (1 950 $) par an dans le cas n° 1, mais dans le cas n° 5, elle permet d'économiser environ 25 000 € (32 500 $) par an par rapport à la solution A. 5, elle permet d'économiser environ 25 000 € (32 500 $) par an par rapport à la solution A. En évaluant le cas n° 1, on peut se demander comment la solution A - qui est capable de fournir exactement le débit d'air demandé par le système sans aucun soufflage d'air - a presque la même efficacité que la solution C. La réponse est révélée dans les figures 13 et 14.
La figure 10 compare la puissance spécifique à 8 bar de différents modèles centrifuges avec celle de grands compresseurs à vis à vitesse variable². Un compresseur centrifuge de 75 m3/min fonctionnant au point de conception est 19 % plus efficace qu'un compresseur à vis à vitesse variable de 500 kW ; un compresseur centrifuge de 115 m3/min est 14 % plus efficace qu'un compresseur à vis à vitesse variable de 700 kW ; et un compresseur centrifuge de 140 m3/min est 19 % plus efficace qu'un compresseur à vis à vitesse variable de 900 kW.
Fig. 10 : Comparaison de la puissance spécifique de l'emballage à 8 barg
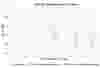
CONSIDÉRATIONS RELATIVES AUX COMPRESSEURS CENTRIFUGES
En résumé, seule la connaissance du poids ou de l'équilibre réel, en termes de pourcentage de temps ou de conditions de fonctionnement variables, permet aux opérateurs de déterminer si le grand compresseur d'air à vis à vitesse variable est adapté au système. Il s'agit d'un concept important qui est souvent négligé ou mal compris. Nous allons utiliser un autre cas réel pour clarifier ce concept.
Un client possédait cinq vieux compresseurs centrifuges de 4 bar de différentes tailles allant de 70 m3/min à 120 m3/min. L'année dernière, il a décidé de moderniser la salle des compresseurs afin de réduire les coûts d'exploitation. Il a indiqué qu'un audit avait été réalisé et que la première étape consistait à améliorer l'efficacité de leur système. Pour ce faire, il a décidé de remplacer un compresseur centrifuge par un compresseur d'air à vis à vitesse variable de 500 kW.
Après une enquête plus approfondie, ils ont constaté que certains matins, entre 8 et 10 heures, le fabricant devait arrêter une ligne de production pour préparer le type de verre à produire le lendemain. Pendant ces deux heures, ils ont eu un excès d'air de 60 m3/min. Comme l'ancien compresseur centrifuge ne pouvait réguler que 20 m3/min, le compresseur centrifuge soufflait 40 m3/min d'air. En remplaçant ce compresseur par un compresseur à vis à vitesse variable de 500 kW, il aurait été possible d'éviter toute fuite, d'améliorer l'efficacité du système et de réduire les coûts d'exploitation.
Malheureusement, il s'agit là d'une approche erronée et trompeuse. Il est vrai qu'un compresseur à vis à vitesse variable de 500 kW permettrait d'éviter les purges pendant les périodes d'arrêt de l'usine, mais le client n'a pas envisagé une comparaison réelle des performances, comme le montre la figure 12. Le client aurait dû effectuer une comparaison des coûts énergétiques entre un nouveau compresseur centrifuge à deux étages et le compresseur à vis à deux étages de 500 kW à vitesse variable qu'il souhaitait.
Fig. 12 : Comparaison de la puissance spécifique du boîtier dans la plage de régulation à 4 barg
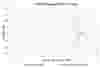
On peut déduire des fiches techniques des compresseurs qu'à une pression de fonctionnement de 4 bar, un compresseur à vis à vitesse variable de 500 kW est 43 % moins efficace qu'un compresseur centrifuge équivalent. Même si le compresseur centrifuge souffle 13 m3/min, il est plus efficace que le compresseur à vis à vitesse variable.
Pour déterminer la meilleure machine pour l'application, le client aurait dû évaluer le coût du soufflage de 40 m3/min pendant deux heures par jour et calculer le coût supplémentaire de l'utilisation d'un compresseur qui est 43% moins efficace pendant les 22 heures restantes de la journée.
Les calculs révèlent que
Coût de la purge :
40 m3/min × 4,3 kW/m3/min × 2 h/j × 350 j/an × 0,10 € (0,13 $)/kWh ≈ 12.000 € (15 600 $)/an
Coût supplémentaire pour comprimer 80 m3/min pendant 22 heures/jour avec un compresseur 43 % moins efficace :
80 m3/min × (6.0 - 4,2) kW/m3/min × 22 h/j × 350 j/an × 0,10 € (0,13 $)/kWh ≈ 110 000 € (144 000 $)/an³
Pour éviter de gaspiller 12 000 € (15 600 $) par an à cause de la purge pendant les temps d'arrêt prévus, le client aurait dépensé 110 000 € (144 000 $) par an de plus, en faisant fonctionner un compresseur 43 % moins efficace pendant le reste de la journée. Même si l'on considère que 22 heures par jour le compresseur à vis à vitesse variable ne fonctionne pas toujours à pleine charge, la différence est si importante qu'il serait difficile d'affirmer que le client aurait économisé de l'énergie et de l'argent en achetant un compresseur à vis à vitesse variable de 500 kW au lieu d'un nouveau compresseur centrifuge.
CONCLUSIONS
Les cas analysés dans cet article montrent que lorsqu'un système d'air nécessite de grandes quantités d'air (environ >100 m3/min) et que la demande d'air fluctue fortement au cours de la journée, l'utilisation de grands compresseurs à vis à vitesse variable (300-400 kW et plus) représente rarement la solution magique souvent revendiquée par certains fabricants de compresseurs. Des technologies ou des solutions alternatives, comme le compresseur centrifuge avec contrôle de la répartition de la charge, permettent souvent aux opérateurs de réaliser des économies d'énergie bien plus importantes, malgré la purge d'air du système.
En fait, les compresseurs centrifuges peuvent être plus efficaces que les grands compresseurs à vis à vitesse variable, même s'ils perdent 10 à 15 % de leur capacité nominale. Plutôt que d'évaluer si une technologie de compresseur réduit les pertes d'air comprimé, il est recommandé aux opérateurs d'évaluer l'efficacité du compresseur sur sa plage de fonctionnement, c'est-à-dire à pleine charge et à charge partielle.
Tout d'abord, il est important de connaître le profil et le spectre exacts du débit du système afin de déterminer combien de temps le compresseur fonctionnera dans une condition par rapport à une autre, par exemple en évacuant un peu d'air ou en fonctionnant à un niveau proche de sa capacité nominale. C'est pourquoi il est important de procéder à une évaluation de la qualité de l'air avant de commencer toute évaluation. Les résultats doivent être lus et interprétés correctement - et non pas exploités pour justifier la vente d'un compresseur !
Néanmoins, chaque cas est spécifique et plusieurs aspects susceptibles d'influencer le choix final doivent être pris en compte : les exigences d'installation, l'espace au sol, la nécessité d'unités de secours et/ou d'un stock de pièces détachées, la flexibilité du système en cas de besoins de production futurs différents et l'investissement initial en capital. L'investissement initial a été intentionnellement exclu de cette étude, car l'objectif était d'évaluer les systèmes du point de vue de la consommation d'énergie uniquement. L'investissement initial et la période de retour sur investissement détermineront la décision finale. Sans entrer dans des discussions ou des détails sur les prix, les solutions B et C sont susceptibles d'avoir les investissements initiaux les plus faibles.